Wind generation is a “clean energy” source which is expected to experience the highest growth in the near future among the various renewables. If suitably exploited, wind energy can, in fact, remarkably (although discontinuously) contribute to meet the global electric power demand. Wind energy can be exploited at different levels and in different ways, ranging from off-shore wind farms to micro-wind generators to be installed in domestic and urban environments. All the applications, however, call for special electric generators to be coupled to wind turbines. Such generators need to be carefully sized and designed to meet application requirements, which often include demanding constraints in terms of size, noise, vibration and wide-speed-range operation.
The Dept. of Engineering and Architecture - DIA at the University of Trieste has taken part in various research projects intended to develop new wind generator prototypes, mainly in cooperation with InterWind and with Nidec-ASI.
The cooperation with InterWind raims at developing micro-wind generators of “ MAIA” series, with power ratings around 3 kW and rated speeds around 400 rpm, suitable for household installation. Personnel of DIA Dept. has supported the company in assessing the electromagnetic design of the micro-wind electric generator and exploring the optimization margins, specifically with respect to the best shaping and positioning of rotor permanent magnets in view of machine performance optimization.
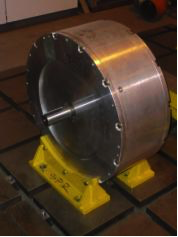
The cooperation with Nidec-ASI in the field of micro-wind applications has been intended to develop and innovative electric generator prototype rated 20 kW at 1200 rpm.
The main design challenge faced in developing the generator has been to make it fit for operation even in very weak wind conditions, hence at very low torque and speed. For this purpose, it has been necessary to eliminate the so-called “cogging torque”, which is the parasitic torque arising due to the magnetic interaction between permanent magnets and the stator slots and teeth. The cogging torque is detrimental at low speed and power operation as it may prevent the turbine to spin and cause unwanted stops.
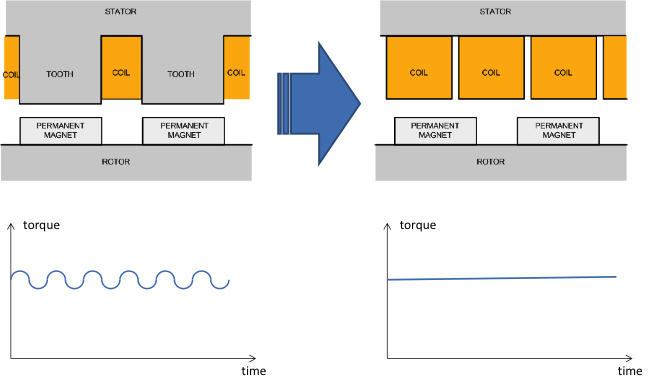
Since permanent magnets had to be maintained in order to meet the required size constraints, the design provision which has been adopted has been to move from a conventional “slotted” design (with teeth and slots) to a “slotless” design (Fig. 3) where the machine windings are directly attached to the smooth inner bore of the stator core, shaped as a ferromagnetic hollow cylinder (Fig. 4).
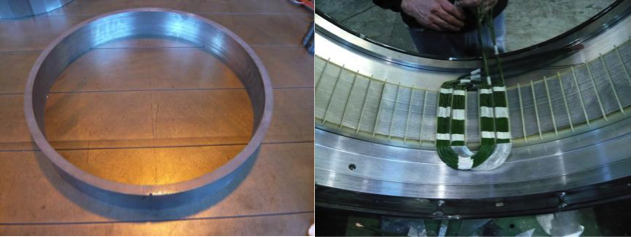
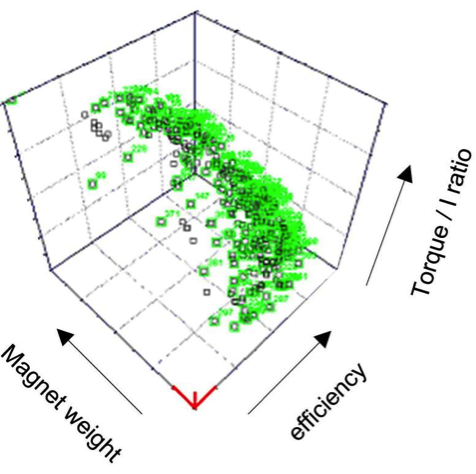
The electromagnetic design of the slotless prototype has called for a multi-objective constrained optimization design procedure based on genetic algorithms. Some design variables have been identified along with size and performance constraints as well as suitable objective functions relating to machine efficiency, current rating and permanent magnet weight.
From the inspection of the best design solutions (Pareto front) it has been possible to identify the fittest design values to meet specifications with the machine minimum weight, cost and size. The manufactured prototype has been successfully tested by Nidec-ASI.
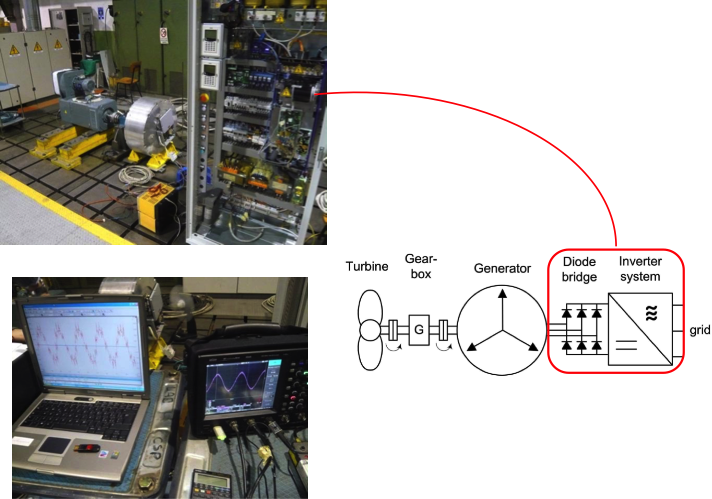
Further details on the project can be found in the following paper:
http://ieeexplore.ieee.org/stamp/stamp.jsp?tp=&arnumber=6036339.
For more information, please contact dr. Alberto Tessarolo.